Ridgeback Integration
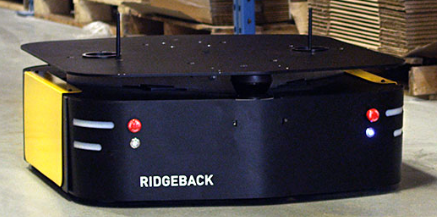
To attach custom hardware to Ridgeback, you will have to take care of mechanical mounting, electrical supply, and software integration. This guide aims to equip you with respect to these challenges.
Mechanical Mounting
When determining mechanical mounting, you can use the Standard mounting pattern on the Ridgeback. At this time, the "PACS™" mounting system is not available for Ridgeback.
Mechanical, Standard
The payload integration plate can be used to mount external payloads on top of the Ridgeback. The plate is made of aluminum, which allows Ridgeback to support payloads up to 100 kg (220 lbs). Ridgeback's batteries are positioned low in the chassis and slightly rearward of center of the robot to balance the weight distribution when mounting front-facing manipulator payloads. To minimize the possibility of tipping over, payload structures should always be mounted as close to center as possible.
Payload Mounting Holes
Located at the front-end of the mounting plate are two 5/8"-11 screw holes for mounting Baxter, UR5/UR510 manipulator arms, or any other payload structure. These holes are indicated in the figure below. If you purchased the Baxter or UR5/UR10 package from Clearpath Robotics, Ridgeback will come with the required hardware adapters to securely mount the payload structures to the plate.
If your payload structure requires additional mounting holes or a different hole configuration, the plate can be removed and additional holes can be drilled. To remove the mounting plate, simply remove the screws that form the diamond pattern on top of the plate.
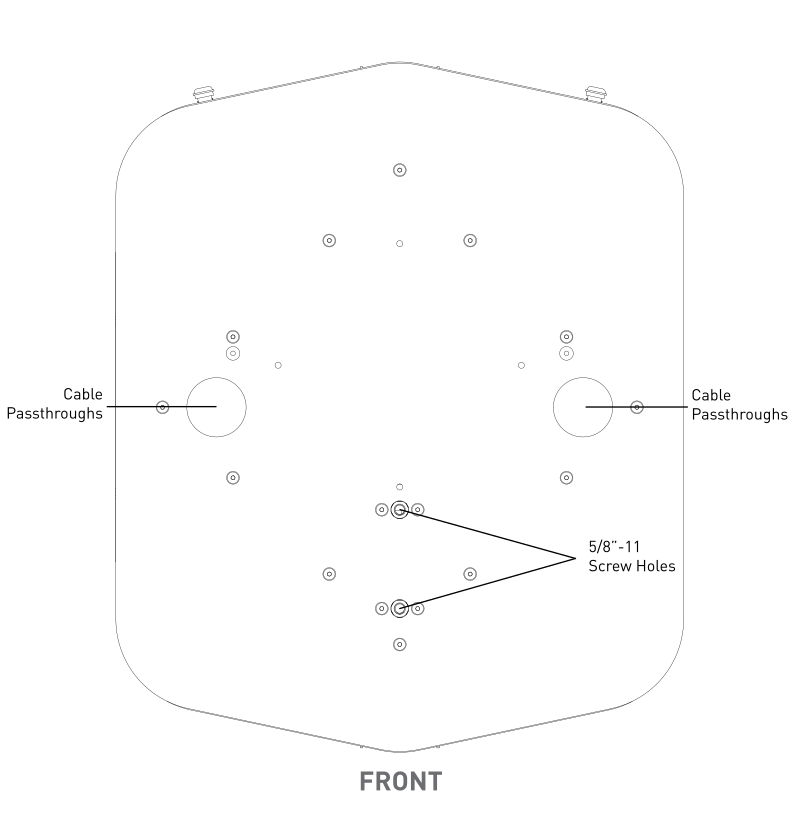
Permanent damage resulting from custom modifications to the mounting plate is not covered under warranty and may not be supported by Clearpath Support. Please contact our support team if you require assistance or have any questions relating to custom modifications.
Electrical Integration
Except for bus-powered USB cameras, most payloads have separate leads for power and data.
Data Connections
The two larger holes on the left and right side of the payload integration plate allow you to pass electrical wires and cables from the mounted payloads into the User Bay. Electrical wires should always pass through the provided plastic grommets to protect against cutting and abrasion.
Ridgeback's internal computer options support USB3 and Ethernet connectivity.
An Ethernet switch or PoE power injector can be added to the User Bay as required.
Connector Summary
Several user power connectors are accessible in the User Bay for powering user payloads. These are summarized in the following table and described in more detail in the following sections. The power rails on the User Bay Power board are protected against short circuit by fuses. See the illustration for the connector and fuse locations.
- For the High Current VBAT User Power (labelled as 24 VDC, 20 A MAX), terminate your payload's power lead with the appropriate Anderson connectors.
- For the User Power Ports, terminate your payload's power lead with the appropriate crimps and pins. for the four pin Molex connector. The maximum current draw permitted on each rail is 5A.
- For the Inverter Power, terminate your payload's power lead with the appropriate Anderson connectors.
Port (see Figure) | MCU board connector | Mating connector | Crimp terminals | Crimping tool |
---|---|---|---|---|
High Current VBAT User Power | Anderson PP15/45 1327-BK (red) + 1327G6-BK (black) + Anderson 261G2-LPBK | Anderson PP15/45 1327-BK (red) + 1327G6-BK (black) | Anderson 262G2-LPBK (AWG 16-20) or 261G3-LPBK (AWG 10-14) | Anderson 1309G8 |
User Power Ports | Molex 0039301040 | Molex 0039012040 | Molex 0507528200 (AWG 20-22) or Molex 0503518100 (AWG 22-28) | Molex 2002184900 |
Inverter Power | Anderson 1327G8-BK (blue) + 1327G6-BK (black) | Anderson 1327G8-BK (blue) + 1327G6-BK (black) | Anderson 262G2-LPBK (AWG 16-20) or 261G3-LPBK (AWG 10-14) | Anderson 1309G8 |
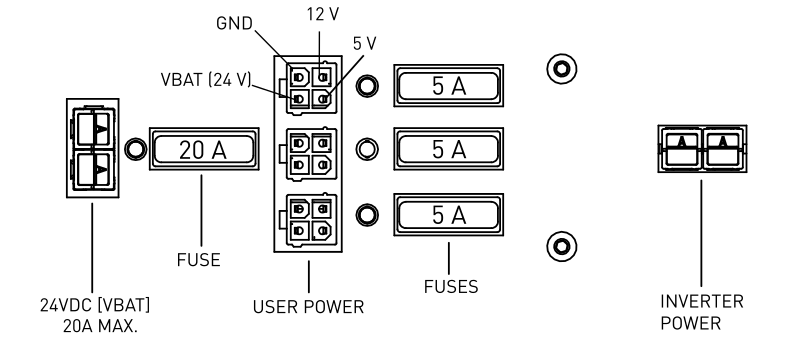
User Power Connections
Similar to the data connections, power leads may be brought through the two larger holes on the left and right side of the payload integration plate, and connected to the power ports in the User Bay. The following are available as user power:
- Unregulated VBAT power (25.6 V nominal) available in two ways:
- High Current VBAT User Power (20 A max)
- User Power ports: 5 A, shared across the User Power ports
- Regulated 12 V power: 5 A, shared across the User Power ports
- Regulated 5 V power: 5 A, shared across the User Power ports.
Each User Power Port (Molex 0039301040) has a shared ground (GND) pin with a maximum current rating of 8 A. Ensure that the combined current draw for the VBAT, 12 V, and 5 V pins for the corresponding GND pin does not exceed 8 A.
The unregulated battery output may range from as low as 20 VDC up to 30 VDC depending on the state of charge of the battery and the electrical loading on the system. Ensure any accessories connected to that rail are able to deal with unregulated battery voltages.
For continued protection against risk of fire, always replace fuses only with those of the same type and rating.
Optional External Motion Stop
In addition to the built-in Motion Stop button, an external motion-stop latching button/switch can be added that has similar functionality.
Electrically, the external motion-stop latching button/switch can be connected to the 4-pin MCU connector labelled E-STOP BREAKOUT
using
a mating connector. This 4-pin connector is the same as the one used for the User Power Ports. Refer to
Connector Summary for details.
The four pins should be connected as follows:
- 1-2: to external motion-stop breakout
- To engage motion-stop: press and release the latching button/switch (3.3 V)
- To clear motion-stop: ensure the button is released on the external motion stop, then press and release the Motion Stop button on the Ridgeback unit to clear the motion-stop
- 3-4: short these pins to indicate that external motion-stop is present
Software Integration
ROS has a large ecosystem of sensor drivers, some of which include pre-made URDF descriptions and even simulation configurations. Refer to Sensors supported by ROS.
For the best experience, consider purchasing supported accessories from Clearpath Robotics for your robot, which will include simulation, visualization, and driver support.
Refer to the following for more details:
Support
Clearpath is committed to your success. Please get in touch with us and we will do our best to get you rolling again quickly: <support@clearpathrobotics.com>.
To get in touch with a salesperson regarding Clearpath Robotics products, please email <research-sales@clearpathrobotics.com>.
If you have an issue that is specifically about ROS and is something which may be of interest to the broader community, consider asking it on Robotics Stack Exchange. If you do not get a satisfactory response, please ping us and include a link to your question as posted there. If appropriate, we will answer on Robotics Stack Exchange for the benefit of the community.